Solicitations during lifetime
A satellite’s life is one of survival against some of the harshest conditions known to engineering. From conception on Earth to the extremes of space and finally its re-entry into the atmosphere, each satellite faces a unique set of challenges. Engineers take every possible measure to ensure that satellites not only survive but operate efficiently throughout their journey. Here’s an in-depth look at these stages, comparing each environment’s challenges to make them easier to understand.
On Earth: A Safe, Yet Sensitive Start
While still on Earth, a satellite is in the safest environment it will ever know. Satellites are manufactured in what’s known as a “clean room”, a highly regulated space with controlled humidity, temperature, and cleanliness. The purpose is to avoid any contaminants like dust that could affect delicate systems. Think of it like a hospital operating room, an environment where cleanliness is essential for optimal performance.
However, even this safe haven comes with challenges. Once assembled, the satellite is carefully transported, often by boat or plane, to the launch site. By boat, the trip is slow but less jarring, much like a gentle car ride. Air transport, on the other hand, is faster but more stressful, with the satellite subject to higher mechanical strain. This transportation phase, though seemingly straightforward, requires careful handling to protect the satellite’s fragile systems.
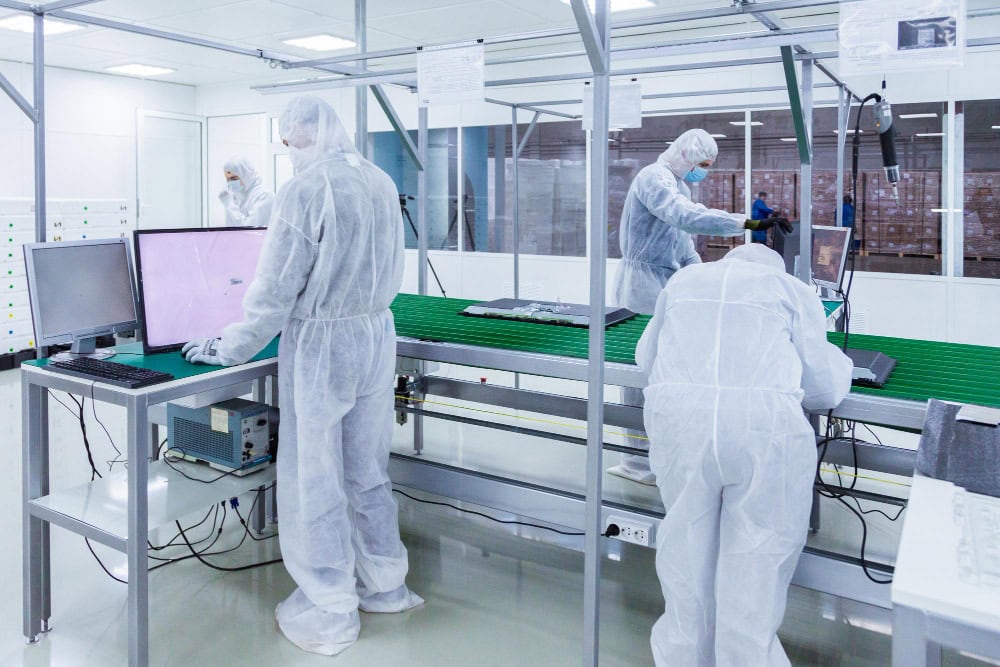
During Launch: A Gauntlet of Extreme Forces
The most intense physical stress a satellite experiences comes during its launch. Imagine riding a roller coaster but with forces hundreds of times stronger. The engines of a rocket, like the Falcon 9 or Ariane 6, produce thrusts of around 7,000 kilonewtons – equivalent to the force needed to lift nearly 700 cars at once. This immense thrust creates violent vibrations that shake the satellite to its core.
One major hazard here is resonance. In simple terms, resonance happens when the vibration frequency from the rocket engines matches the natural frequency of the satellite structure, which can amplify the vibrations to dangerous levels. This is the same effect that famously led to the collapse of the Tacoma Narrows Bridge in 1940, when wind-induced resonance caused the bridge to sway until it tore apart. To guard against this, satellites undergo rigorous vibration tests to ensure they can withstand launch stresses.
The “pogo effect” is a phenomenon that mostly impacts liquid-fueled rocket engines, as solid propellants are less prone to instability during combustion. The name comes from the pogo stick, a toy that compresses and stretches along its axis as it bounces – similar to what happens to a rocket experiencing this effect.
To understand why this occurs, consider how a liquid engine works. Two separate liquids – fuel (e.g., liquid hydrogen or methane) and oxidizer (e.g., liquid oxygen) – are mixed in the combustion chamber. These liquids flow through distinct pipes from their respective tanks. The ratio of fuel to oxidizer is crucial for efficient combustion. When the ratio is ideal, the exhaust is generating maximum thrust. However, if the ratio shifts (too rich or too lean), combustion becomes less efficient, affecting thrust.
Pressure fluctuations in the propellant pipes can disrupt this ratio, causing a feedback loop: changes in pressure affect combustion, which in turn alters pressure again. This loop creates thrust variations, which lead to vibrations along the rocket’s longitudinal axis, compressing and expanding the structure like a pogo stick.
If these vibrations match the rocket’s natural frequency, resonance occurs, amplifying the effect. To mitigate this, engineers can stiffen or dampen the rocket structure or improve the stability of propellant injection systems.
A resonance demonstration video shows how vibrations intensify at specific frequencies (e.g., around 3.3 Hz), where resonance occurs. Unlike the damped system in the video, rockets are essentially undamped, making them more vulnerable to such effects.
The noise generated during launch is another danger. Sound is a mechanical wave, and at the moment of liftoff, the noise near the rocket engines is intense enough to destroy parts of the rocket if not carefully managed. Water is poured below the rocket at launch to dampen the noise, which instantly turns to steam, creating the familiar massive white clouds seen during liftoff. Even with this, sound levels inside the fairing (the rocket’s protective shell) can reach up to 160 decibels, louder than a jet engine or even a rock concert. This is why satellites are meticulously designed to handle sound-induced vibrations as well.
A final factor here is sloshing, a phenomenon that affects both the rocket and the satellite. The propellant tanks in rockets are not always perfectly steady, and as the rocket launches, the fuel can move back and forth, creating small jerking motions. The movement of the liquid propellants in the tanks also induces momentum/inertia into the rocket, making it drift a bit and altering its trajectory if not corrected by the GNC (Guidance, Navigation and Control system). This is like the sudden shifts you feel in a car if the driver doesn’t press the clutch smoothly. In satellites with liquid fuel onboard, sloshing can place additional stress on the walls of the fuel tanks, which could cause damage if they are not built to absorb it.
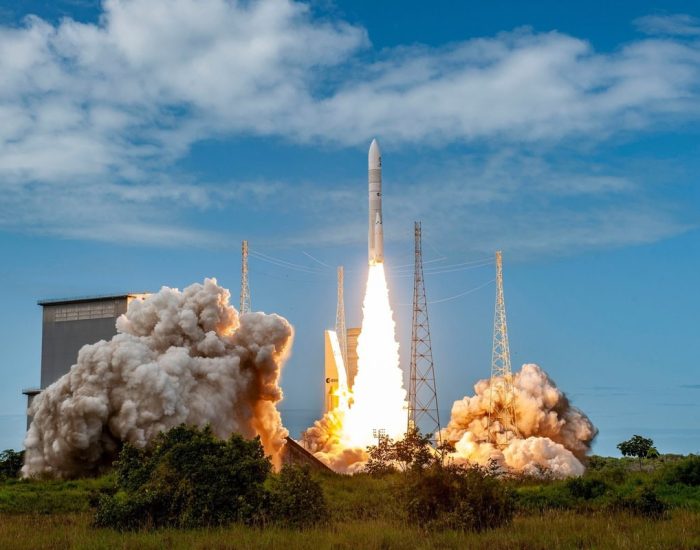
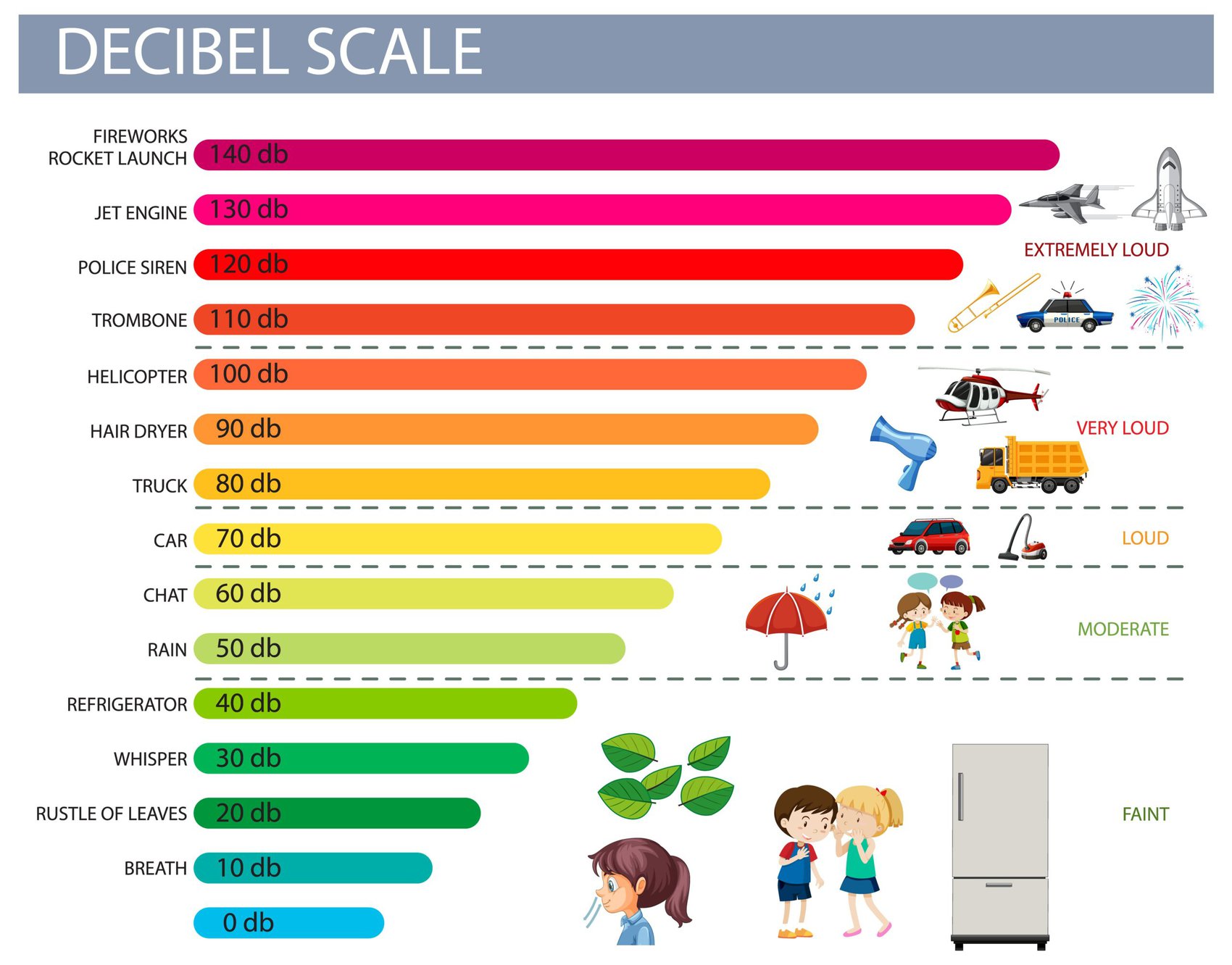
Operating in Space: Heat, Cold, and Radiation
Once safely in orbit, a satellite faces an entirely new set of challenges, especially from the Sun. In space, there’s no atmosphere to moderate temperature, so satellites experience extreme heat when in direct sunlight, up to 120°C (248°F), and bitter cold when in Earth’s shadow, as low as -180°C (-292°F). Imagine if your phone were left outside in these temperatures, it would shut down immediately. Satellite materials are chosen to withstand these swings, and their components are designed to expand and contract without breaking.
Beyond temperature, the Sun also emits harmful radiation, especially intense in areas like the Van Allen radiation belts. These belts are regions around Earth filled with charged particles from the Sun, which can damage satellite electronics. To protect against this, satellite engineers use advanced shielding, often made of multi-layer insulation, lightweight polymers, and aluminum. Unlike the thick lead shielding used in nuclear reactors, these materials balance weight and protection, allowing the satellite to shield itself without adding excessive mass, which is crucial during launch and operation.
The risk of collision with space debris is another growing concern. Satellites orbit Earth at high speeds, and even tiny pieces of debris, smaller than a grain of sand, can cause damage due to the high relative velocity. Modern tracking systems can monitor objects as small as 1mm across, allowing operators to make minor adjustments to avoid collisions. However, undetectable or sudden debris presents a constant risk in an increasingly crowded orbital environment.
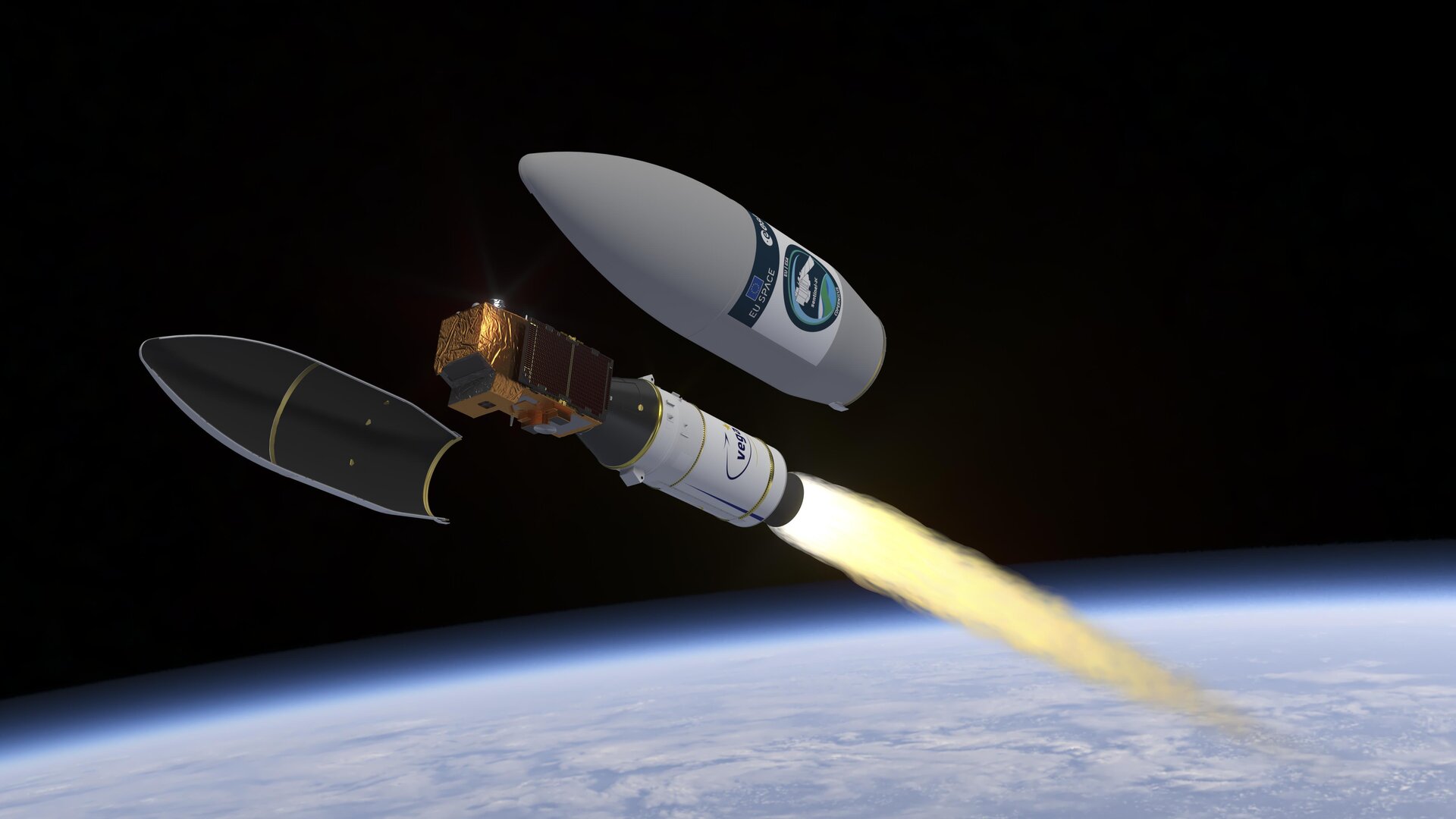
Atmospheric Re-entry: A Fiery Finale
Finally, when a satellite’s mission is over, it must be responsibly deorbited to avoid adding to space debris. At Sternula, we follow ESA’s “5-year rule”, which mandates that satellites in Low Earth Orbit (LEO) either re-enter the atmosphere or move to a safe “graveyard” orbit within five years after the end of their operational life. For our LEO satellites, atmospheric re-entry is the preferred method.
As a satellite descends, it encounters denser parts of the atmosphere, generating intense friction. This friction heats the satellite’s surface to thousands of degrees Kelvin, comparable to the Sun’s surface temperature. Under these conditions, dioxygen (O2) and dinitrogen (N2) dissociate to become atomic oxygen (O) and atomic nitrogen (N), and can even ionize, meaning that they become ions, the air becomes a conducting medium and turns into plasma: the air is literally on fire.
For crewed re-entry vehicles, heat shields protect the structure, but our satellites are designed to burn up entirely, ensuring that no debris reaches Earth’s surface.
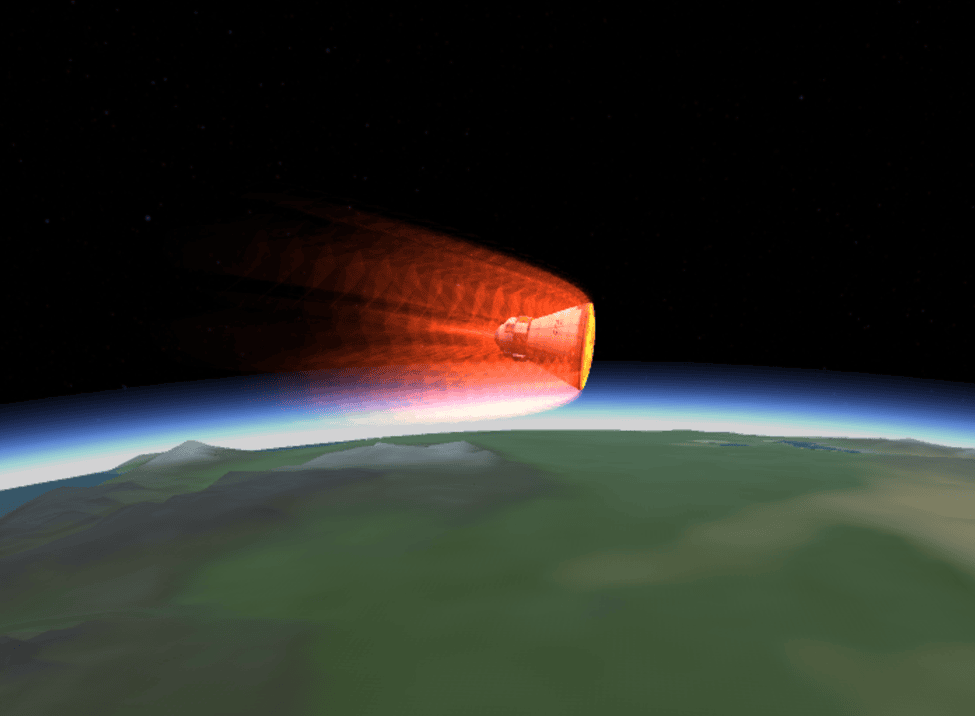
Published on 06/12/2024, Written by: Cyriaque Guillot, Ivan Conti